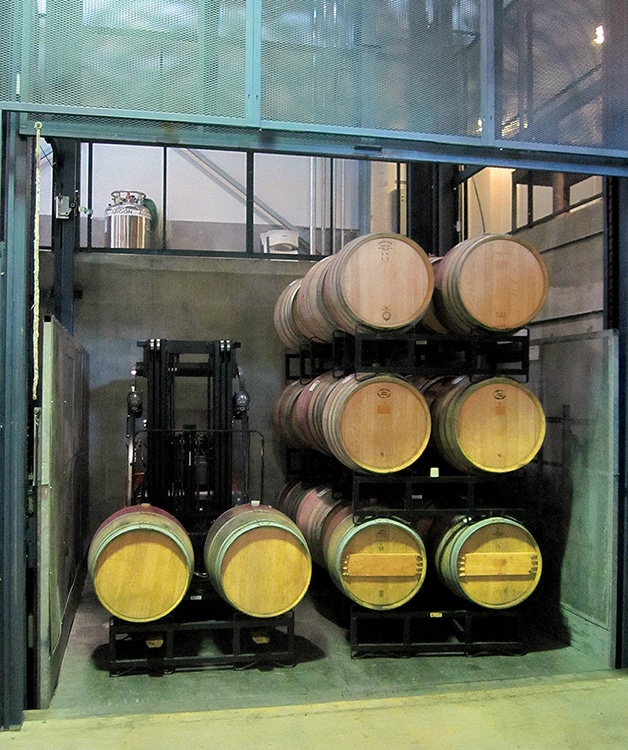
Strength, safety, and customizability make vertical reciprocating conveyors (VRCs) a natural choice for almost any material handling challenge. In fact, the flexible design and scalability mean they have been put to work on an amazing variety of tasks. Let's take a closer look at just a few special applications for vertical reciprocating conveyors around the world.
Raising Expectations: 10 Special Applications for Vertical Reciprocating Conveyors
Vertical Reciprocating Conveyors (VRCs) are made to move material loads of almost any weight, shape, or size vertically between floor levels and can raise or lower materials just a few inches to 200 feet or more. They can move loads at rates anywhere from 18 feet per minute to 400 feet per minute, and align moving surfaces within a fraction of an inch.
VRCs are designed to be less costly to operate and easier to maintain than freight elevators, while still delivering smooth motion to protect the most sensitive products. Available in straddle, cantilever, or 4-post configurations, they can be fully integrated into existing infrastructure, existing elevator shafts, or new construction, and can be designed to fit your space.
PFlow pioneered the VRC concept in the 1970s. Since then we’ve installed both mechanical and hydraulic VRCs in places such as power plants, warehouses, factories, hangars, and automotive showrooms around the world. Today, VRCs continue to help companies make better use of their available space, day in and day out.
The design versatility of VRCs and the ability to put them to work in almost any space or environment has seen them being used in some pretty interesting places.
1. Added Lift for Boeing’s Wings
To lift fragile aircraft wing parts up to 20 feet long at Boeing’s commercial aviation plant in Huntington Beach, CA, PFlow designed a mechanically powered four-post VRC able to accommodate an entire articulated tow truck plus trailer in a 10×40-foot carriage.
The jumbo-sized F Series lift moves this hefty but delicate cargo 20 vertical feet, up to 10 times per day and has built-in protection to guard against accidental tow truck and cart impact.
2. Targeted Solution for Lockheed Martin
Safety and precision were essential when Lockheed Martin asked PFlow to develop a specialized system to handle missiles at the defense contractor’s final assembly and storage plant.
The mission-critical system moves air-to-ground missiles laterally and then vertically from the plant’s production areas into a special testing area. Horizontal and vertical positioning needed to be accurate to within 1/8”, and the F Series-based system needed to conform to the highest standards for moving sensitive and potentially explosive cargoes.
3. On a Roll
“Paperwork” doesn’t come much bigger than the 9,000lb bulk paper rolls a PFlow VRC handles at a plant in Appleton, WI. PFlow created a specially cushioned, tilting F Series VRC for the plant which was designed to safely load, lift, and offload up to 30 rolls per hour.
At the other end of the paper supply chain, we also created a fully integrated VRC solution for Georgia Pacific’s Palatka facility in northern Florida. The 3,000 lb-capacity unit moves finished paper products safely and efficiently from the upper manufacturing level to a ground-level shipping floor, helping to double capacity at the plant.
4. Shell’s Offshore Investment
VRCs are known for their ability to handle tough, challenging environments. That’s why Shell Oil chose a modified PFlow M Series lift to serve a helipad perched atop one of its platforms in the Gulf of Mexico.
The 1,500lb-capacity unit needed to be tough enough to withstand years of high winds and super-corrosive sea air, while also meeting the strict safety protocols required aboard offshore platforms producing highly flammable gas. That meant 100%-spark-free operation, full shielding of all electronic components, and absolutely no on-site welding during installation.
5. Steamy Situations
The same skills PFlow uses to create equipment for saltwater environments like offshore installations and dry docks help us when building VRCs for “wash down” applications such as chicken processing plants. These include waterproof stainless steel control panels with slanted tops to shrug off water and protect against constant exposure to heat and steam.
The extreme cold storage required to store poultry and meat products also creates a challenging operating environment. PFlow delivered a hydraulic VRC solution for Tyson Foods that ensured uninterrupted equipment service, even in the plant's sub-zero temperature environment.
6. Raising a Glass
Nothing beats an ice-cold beer on game day, but vendors were struggling to keep Dolphins' fans refreshed at the team’s Miami stadium. Keeping up to 40 busy beer stands supplied with individual chilled kegs in the oppressive Florida heat was proving to be a challenge.
PFlow worked with Birmingham, Alabama-based Trammell Equipment to install a purpose-built 5,000lb-capacity VRC system capable of moving up to eight half-barrel kegs at a time to any of the four centralized refrigeration stations, from where the brew is piped directly to hard-working taps around the stadium. That’s quite a beer run!
7. Vintage Solution for JPV
PFlow’s lifting skills don’t stop at beer. Joseph Phelps Vineyards (JPV) makes wine in a traditional facility carved into a hillside in Napa Valley, CA. The “gravity-fed” arrangement allows the juice from crushed, de-stemmed, and processed grapes to flow ever deeper into the cool stone of the hillside as it is fermented and then aged in oak barrels stored deep underground.
While gravity helps make the wine, it also makes for a lot of work moving equipment, barrels, and bottles to and from the lowest levels of the winery. PFlow worked with local dealer DW Nicholson and the project’s architects to install a VRC capable of moving fully loaded forklifts to the winery’s lowest levels, while also meeting California’s stringent seismic codes.
8. Discreet Entrance
To help a Milwaukee area funeral home deliver services while protecting their vehicles from the area’s harsh winter weather, PFlow helped design and install an 8,000lb-capacity Series F lift capable of safely lowering and raising hearses and a full-size van to a basement-level facility.
The 10×22-foot lift is used between 12 and 15 times per day, providing easy access to valuable basement-level storage.
9. Far-Sighted Decision for the LSST
For the Large Synoptic Survey Telescope (LSST) project in northern Chile, the National Science Foundation and the Department of Energy selected PFlow to deliver a unique VRC system for safely moving and repositioning the facility’s massive 27-foot primary mirror and opening and closing the observatory’s 20,000-lb roof.
PFlow designed an 80-foot lift with a 35×35-foot carriage with multiple fail safes to allow the mirror to be removed from the top level of the observatory for periodic recoating. This truly unique VRC allows the telescope’s mirror to be moved smoothly and accurately into position but is robust enough to withstand both high winds and seismic shocks up to 8.0 on the Richter scale.
10. Big Bertha
Tradition is everything at the Darrell K Royal-Texas Memorial Stadium in Austin, home of the University of Texas Longhorns. When a stadium remodeling project meant that the Longhorn’s iconic Big Bertha drum—the world’s largest bass drum—might not be able to enter the stadium along with the band on game day, PFlow sprang into action.
Working with Dallas-based Materials Handling Company Cisco-Eagle, PFlow created a VRC capable of lifting a 10×19-foot section of the stadium concourse to create enough clearance in the field-level entrance below for Big Bertha to make it into the stadium. The VRC lifts the 12,000-lb section within 30 seconds to allow Bertha to enter and exit the arena without missing a beat!
It’s Hard to Beat a PFlow VRC
Not to bang our own drum, but it’s difficult to imagine an environment or application where a VRC could not be put to work. If you have a particularly challenging material lifting task, or if you simply want to harness the proven strength, reliability, and flexibility of a PFlow VRC for your operation, contact us today. Our knowledgeable sales and service team is waiting to hear from you.
And, as you can see, we love a challenge. Contact us today, or click below to learn more about the amazing things you can do with a PFlow VRC.