Are you looking to enhance your facility’s material handling capabilities? Vertical reciprocating conveyors (VRCs) are a material handling game changer for any industry, offering efficient and safe movement of materials between floor levels.
As the leading manufacturer of VRCs, PFlow recognizes that a well-designed system is crucial for your operations. By taking key design considerations into account, we ensure that your VRC solution not only meets your current needs but also adapts to future challenges. This thoughtful approach will enhance efficiency, improve safety, and ultimately provide lasting benefits to your operations for years to come.
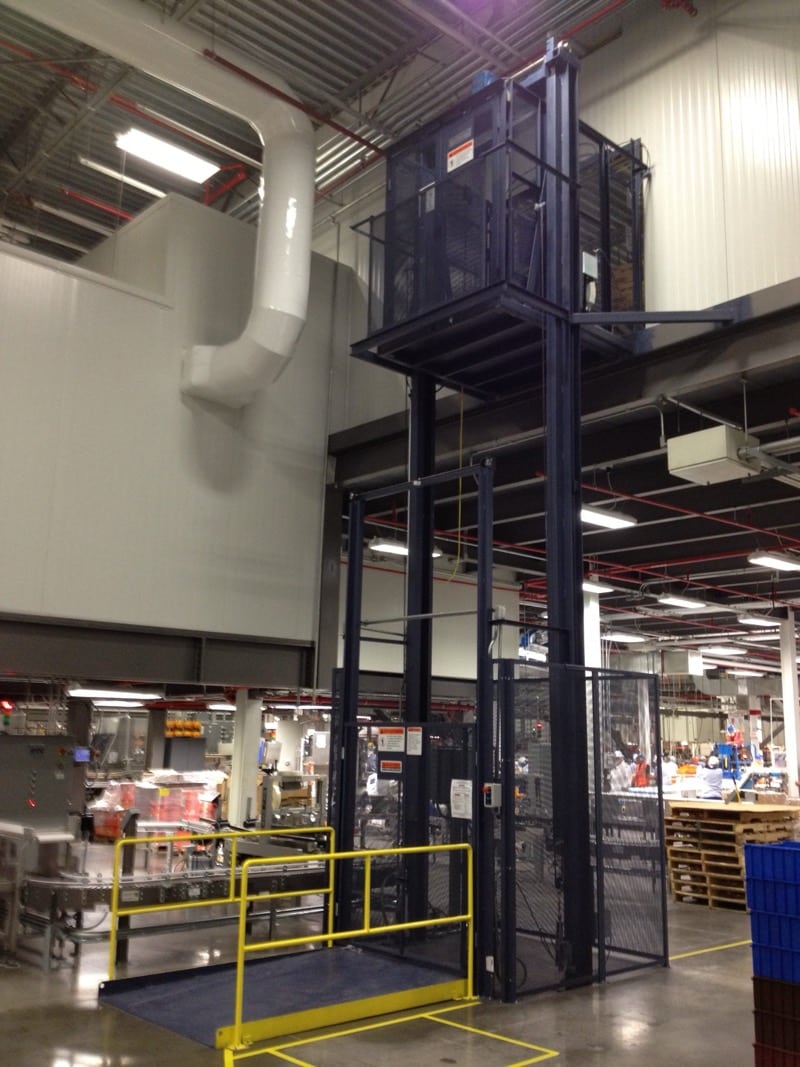
1. Review Workflows
Whether you are incorporating a VRC (or VRCs) into new construction or are looking to add them to your existing facility, it is essential to thoroughly review your current state and desired state workflows to ensure the VRC solution design aligns with your operational needs. By evaluating the key considerations below, PFlow can design a VRC that supports your current needs and future growth:
HOW HIGH?
What is the total vertical rise? (How many feet does the material need to be lifted?) What is the distance from floor to floor? What is the clearance above the upper level?
HOW OFTEN?
How many times per hour will the VRC carry the load? Will it have automatic in-feed and discharge, or manual?
HOW HEAVY?
How much is the maximum total load weight?
HOW BIG?
What are the dimensions of the largest and smallest loads to be lifted? Does the load overhang the pallet? Will there be multiple loads put on the carriage at one time?
HOW NOW?
How is the material currently being moved? Is a VRC currently in use? Is a forklift being used to lift materials? Is there a potential safety hazard?
LOADING PATTERN?
C – Inline
Z – Pass-through
90º – Left/Right
GATES & ENCLOSURES NEEDED?
Will the lift be in a shaft-way?
Will the lift penetrate a floor level?
Will the lift service the shaft-way?
Will the lift service the perimeter (edge) of a
mezzanine?
FLOOR OPENING / SHAFT-WAY?
If the lift is going through a floor or existing man-shaft-way, what are the dimensions of the opening?
2. Material Selection
At PFlow, we focus on delivering solutions that meet your unique operational needs. We understand that the materials used in your VRC are vital for durability and performance.
By sharing your specific environment with us—whether it’s a wash-down area requiring stainless steel, outdoor settings needing hot-dipped galvanized finishes, or hazardous locations that demand explosion-proof components—we can provide customized material options that fit perfectly.
Our commitment to quality, combined with the right material choices, minimizes downtime and maximizes equipment lifespan, ensuring smooth and safe operations that boost your overall efficiency. Your success is our priority!
3. Safety Features
Safety is paramount for any material handling operation and VRCs can deliver an unmatched level of worker and goods protection compared to alternative material lifting solutions such as forklifts or manual goods lifting. VRCs are required under ASME B20.1 regulations to have the following safety features:
- Safety Gates: Interlocked gates must be installed at loading and unloading areas to prevent access while the VRC is in operation.
- Emergency Stop Buttons: Accessible emergency stop buttons must be placed at key locations to allow for immediate shutdown of the system in case of an emergency.
- Overload Protection: Systems must have mechanisms to prevent operation if the load exceeds specified weight limits.
- Limit Switches: These are necessary to stop the conveyor at predetermined upper and lower positions, preventing over-travel.
- Safety Barriers: Protective barriers or guardrails must be in place to prevent unauthorized access to the moving parts of the conveyor.
- Signage: Clear safety signage must be posted to inform operators of safe operating procedures and emergency protocols.
PFlow also offers optional safety features such as our DeckLock Safety System which prevents unintended carriage drop caused by overload or brake malfunction, Twin Roller Guides which reduce carriage rocking and ensure level carriage travel and smooth chain spooling, and high-capacity safety cams that prevent carriage free-fall in the unlikely event of a lifting chain break.
These safety features can boost employee morale and can lead to increased productivity, as your team feels secure in their environment.
4. Drive System
When selecting the ideal vertical reciprocating conveyor (VRC) for your application, it’s crucial to understand the distinctions between mechanical and hydraulic VRCs. Both types offer robust and reliable lifting capabilities, but their unique features make them better suited for different operational needs. Understanding these differences will help you choose the best solution for your specific requirements.
Hydraulic vs Mechanical VRCs
Hydraulic VRCs | Mechanical VRCs | |
---|---|---|
Lifting Mechanism | Remote electric pump pressurizes and transfers fluid to the cylinders, lifting the carriage and payload. Releasing fluid allows descent. | Mechanical VRCs are lifted and lowered by heavy-duty roller chains and a gear reducer assembly. |
Cycles per hour | 10 per hour / 100 per day | Unlimited |
Load Capacity | Up to 6,000 lbs | 200,000 lbs + |
Indoor/Outdoor Use | Both | Both |
Vertical Travel | Up to 22’ | Unlimited |
Configurations | Cantilever and Straddle | Cantilever, Straddle, 4-Post |
Applications | Ideal for limited use lifting in environments with no restrictions on the use of hydraulic fluid | Ideal for repetitive or high-use, high-capacity and/or automated operations and for sensitive payload that requires smooth stops and starts |
Standard Travel Speed | Between 17 – 24 FPM* | Between 18 – 60 FPM* |
Maintenance Requirements | Can require more frequent maintenance versus mechanical | Generally lower maintenance requirements than hydraulic |
Controls | Typically, standard push button controls | Push-button or advanced HMI controls with PLC integration |
Cost | Often lower initial cost than mechanical VRCs | Typically, a higher up-front cost than hydraulic VRCs but offers more versatility |
*Feet per minute
Discover more about the key differences between mechanical and hydraulic VRCs to determine which option best suits your needs.
While every PFlow VRC is custom-designed to meet your specific needs, our offerings are anchored in a variety of “base models” that provide a robust foundation for customization. This allows us to efficiently tailor solutions to your unique material handling requirements while upholding the highest standards of quality and performance.
For instance, our B Series and DB Series units are compact, measuring as small as 3’ x 3’, making them ideal for smaller-scale material handling applications. Conversely, there’s virtually no maximum size limit for a PFlow VRC; we can accommodate enormous, sky-high loads and even lift components as large as aircraft wings.
Customers often inquire about the average size of a PFlow VRC. However, since each unit is uniquely built to fit specific load requirements and spatial constraints, the specifications below serve merely as a guideline. Load capacity will vary based on the custom options selected for your VRC.
MODEL | M SERIES | F SERIES | 21 SERIES | D SERIES | B SERIES | DB SERIES |
---|---|---|---|---|---|---|
Type | Mechanical | Mechanical | Hydraulic | Hydraulic | Mechanical | Mechanical (automated with carriage conveyor) |
Carriage Size | Up to 12' W x 10' L | Minimum 6' W x 6'6" L | Up to 12' W x 10' L | 6' W x 6' L | 3' W x 3' L (standard 3' load height) | 3' W x 3' L |
Configuration | 2-Post Cantilever or Straddle | 4-Post | 2-Post Cantilever or Straddle | 2-Post Cantilever | 4-Post, Formed Steel Frame | 2-Post Cantilever |
Capacity (lbs) | Up to 10,000, based on carriage size | Unlimited | Up to 6,000, based on carriage size | Up to 3,000, based on carriage size | 500 | 100 (Small Packages) |
Vertical Rise | Unlimited | Unlimited | Up to 22' | Up to 15' | 15' 9" Floor-to-Floor (30" elevation at each level) | Standard Up to 20' |
Levels | Multi | Multi | 2 | 2 | 2 | Multi |
Standard Speed | 25 FPM | 18 FPM | 24 FPM | 17 FPM | 30 FPM | 60 FPM |
Speed Upgrade | Up to 400 FPM or More | Up to 400 FPM or More | 30 FPM | 25 FPM | – | Up to 400 FPM or More |
Cycles | Unlimited - Continuous | Unlimited - Continuous | 10/Hour - 100/Day | 10/Hour - 100/Day | Unlimited - Continuous | Unlimited - Continuous |
5. Controls
Push Button Controls
Feature: Push button controls offer simplicity and ease of use, allowing operators to quickly activate the system with just a press.
Advantage: This straightforward interface is ideal for facilities with less complex operations or where quick, direct control is paramount.
Benefit: It minimizes training time and enhances user confidence, ensuring your team can operate the VRC efficiently.
HMI Controls
Feature: HMI controls powered by a PLC provide advanced functionality, including programmable settings, real-time monitoring, and diagnostic capabilities.
Advantage: This allows for greater flexibility and control over the VRC's operation, making it perfect for dynamic environments with varying loads and workflows.
Benefit: With HMI controls, you can optimize performance, reduce downtime through proactive maintenance alerts, and improve overall operational efficiency.
6. Special Operational Requirements
Every facility faces distinct operational challenges, and PFlow is here to help you tackle them.
Whether your material lifting needs are indoors, outdoors, in the Gulf of Mexico, in a clean room, or in a wash-down environment, or exposed to extreme temperatures, we provide tailored solutions like full stainless-steel construction, hot-dip galvanized finishes, or epoxy coatings to maximize the lifespan of your VRC.
Need explosion-proof components? We’ve got you covered. With PFlow, you’re investing in durability and reliability, ensuring your operations run smoothly and safely, no matter the environment.
PFlow Industries: Your VRC Design Partner
Investing in a VRC tailored to your facility’s unique needs can revolutionize your material handling operations. By prioritizing critical factors such as workflow design, safety features, drive systems, and control options, you enhance safety, efficiency, and productivity.
With PFlow’s expertise and customized solutions—whether for challenging environments, heavy loads, or specific safety requirements—you’re not just purchasing equipment; you’re securing a reliable partner in your success.
Since pioneering VRCs in the 1970s, PFlow Industries has built, delivered, and supported units of all sizes across diverse industries. Our adaptable VRC designs are powerful, safe, and reliable, ready to tackle almost any challenge while providing dependable lifting capacity. We invite you to discuss your vertical handling challenges with us. From concept to delivery, we’ll partner with you to ensure a fully customized VRC that meets your needs today and into the future. Our commitment extends beyond installation; we provide ongoing support and value-added services throughout your VRC’s lifespan.
Contact us today or click below to discover the best VRC options for your application, and let us help propel your business forward with smooth and safe material movement for years to come.