In the rapidly evolving landscape of logistics and material handling, warehouse technology continues to push the boundaries of operational efficiency and productivity. As we move into 2025, warehouse managers and distribution center leaders are focused on the challenges of automating multilevel warehouses and leaning into a transformative era of technological innovation that promises to reshape how we approach storage, movement, and management of goods.
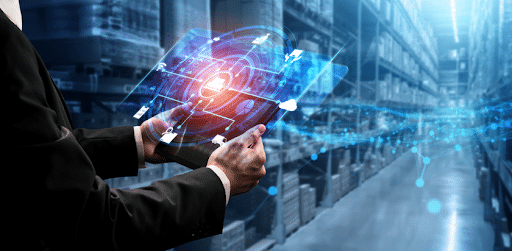
Top Warehouse Technology Trends in 2025
1. Advanced Artificial Intelligence and Machine Learning Integration
Artificial Intelligence (AI) and Machine Learning (ML) are no longer futuristic concepts but practical tools revolutionizing warehouse operations. In 2025, these technologies are providing unprecedented insights into:- Predictive maintenance for equipment
- Inventory optimization
- Real-time demand forecasting
- Intelligent routing and pick and pack strategies
2. Autonomous Mobile Robots (AMRs) and Automated Guided Vehicles (AGVs)
- Seamlessly navigating complex warehouse environments
- Working alongside and collaborating with human workers
- Handling repetitive tasks with enhanced precision
- Reducing physical strain and improving worker safety
3. Internet of Things (IoT) and Real-Time Tracking
IoT technology has become an integral warehouse management tool. It’s transforming warehouse operations by enabling:
- Comprehensive asset tracking
- Environmental condition monitoring
- Real-time inventory management
- Enhanced supply chain visibility
4. Advanced Vertical Storage Solutions
As warehouses look to scale production, vertical space utilization has become a critical focus, with technologies like Vertical Reciprocating Conveyors (VRCs) allowing warehouses to:
- Maximize vertical storage capacity
- Improve material handling efficiency
- Reduce floor space requirements
- Enhance warehouse safety
VRCs are easily integrated into warehouse automation systems, further enhancing operational efficiency.
5. Sustainable Automation Technologies
Environmental considerations are driving innovation in warehouse technology, with trends including:
- Energy-efficient automation systems
- Eco-friendly material handling equipment
- Renewable energy integration
- Reduced carbon footprint solutions
Emerging Trends Beyond 2025
As these new technologies expand their capabilities, they will inspire more groundbreaking developments beyond 2025. Looking further ahead, three technological advancements we anticipate in the future and will be closely monitoring are as follows.
Quantum Computing in Logistics
Quantum computing is expected to revolutionize:
- Complex supply chain optimization
- Instantaneous routing calculations
- Advanced predictive modeling
- Unprecedented computational efficiency
Augmented Reality (AR) Workplace Integration
Future warehouses will likely see AR technologies enabling:
- Advanced worker training
- Real-time guidance and information overlay
- Enhanced equipment maintenance procedures
- Improved worker productivity and error reduction
Hyper-Intelligent Automation Ecosystems
The next wave of warehouse technology will focus on creating fully integrated, self-optimizing systems that:
- Learn and adapt in real-time
- Minimize human intervention
- Provide end-to-end operational intelligence
- Dynamically adjust to changing market conditions
PFlow: Your Trusted Vertical Lifting Partner
In the rapidly evolving world of automated warehouses, PFlow stands as your trusted partner in vertical material handling, providing innovative, reliable, and efficient solutions to meet the demands of modern warehouse automation.
We recognize the complexities of integrating vertical transportation into automated environments. That’s why we collaborate with you to design and implement VRC solutions tailored to your specific needs—enhancing productivity, ensuring safety, and preparing your operations for future advancements.
Looking to optimize your automated warehouse with cutting-edge vertical material lifting solutions? Partner with PFlow, and let our expert engineers guide you in selecting and integrating the perfect VRC for your automated warehouse operations. Together, we’ll elevate your warehouse efficiency to new heights.