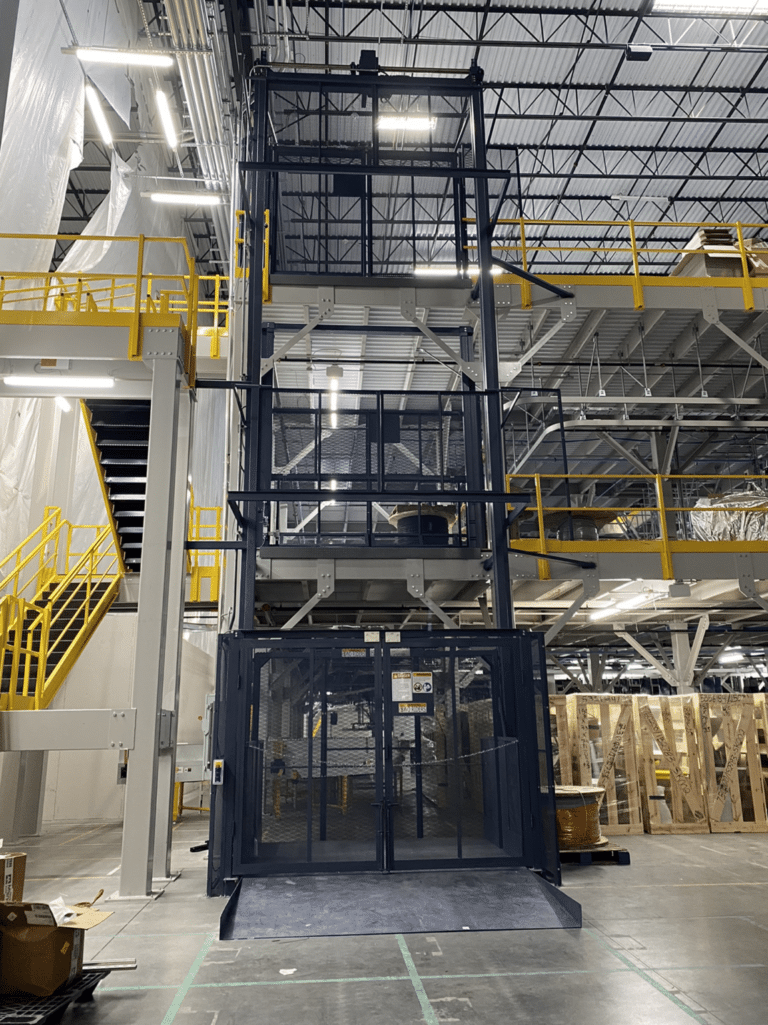
Vertical reciprocating conveyors (VRCs) allow integrated material handling systems to work across multiple levels in today’s automated warehouses.
That’s a critical advantage for companies looking to maximize expensive storage space while reducing material handling, and fulfillment times.
In this article, we examine what goes into ensuring a seamless integration of VRC equipment with existing warehouse automation systems.
We’ll look at why VRC technology offers critical advantages for automated warehouses. Then we’ll review some key planning steps, technical considerations, and industry best practices for integrating VRC equipment successfully with your existing systems and workflows.
Why VRCs for Automated Systems?
VRCs remain the go-to choice for industrial lifting solutions in warehouses and distribution centers, even those with end-to-end automated material handling systems. Here’s why:
- Reliability and Safety: VRCs can repeatedly move loads of 10 lb to 100,000 lb to multiple floor levels. VRCs also include comprehensive standard safety features such as overload brakes and failsafe cams to prevent carriage free-fall.
- Flexibility and Customization: VRCs provide a tailored lifting solution for each application, providing the lifting power and capacity you need to fit your available space. VRCs integrate perfectly within existing facility workflows to work seamlessly with horizontal conveyor systems, processing equipment, and even automated vehicles.
- Cost of Ownership: VRCs bring the power, reliability, and safety of elevator systems to industrial spaces without the associated maintenance and compliance burdens. VRCs can save your facility thousands of dollars in labor, maintenance, and overhead costs every year.
VRCs and Automated Systems: Technical Planning
VRCs deliver the power and dependability needed for effective warehouse automation. Their actual performance, however, depends on how well your VRC is integrated with your existing workflows, especially if you already have an end-to-end warehouse automation system in place.
Failing to properly plan for VRC integration can lead to increased system downtime and even expensive retrofits, which will eat into the cost savings and long-term return on investment that high-quality VRC equipment is designed to bring to your operation.
To prevent this from happening, it’s important to carry out a detailed program of preliminary planning and preparation.
Initial Assessment
Start with the basics. Identify the needs of your warehouse and material handling systems and the specific tasks that your VRC will perform, including:
- HOW HIGH?
- What is the total vertical rise?
- (How many feet does the material need to be lifted?)
- What is the distance from floor to floor?
- What is the clearance above the upper level?
- HOW OFTEN?
- How many times per hour will the VRC carry the load?
- Will it have automatic in-feed and discharge, or manual?
- HOW HEAVY?
- How much is the maximum total load weight?
- HOW BIG?
- How much is the maximum total load weight?
- Does the load overhang the pallet?
- Will there be multiple loads put on the carriage at one time?
- HOW NOW?
- How is the material currently being moved?
- Is a VRC currently in use?
- Is a forklift being used to lift materials?
- Is there a potential safety hazard?
- LOADING PATTERN?
- C – Inline
- Z – Pass-through
- 90º – Left/Right
- GATES & ENCLOSURES NEEDED?
- Will the lift be in a shaft-way?
- Will the lift penetrate a floor level?
- Will the lift service the shaft-way?
- Will the lift service the perimeter (edge) of a mezzanine?
- FLOOR OPENING / SHAFT-WAY?
- If the lift is going through a floor or existing man-shaft-way, what are the dimensions of the opening?
- Integration solution required at each contact point (e.g. VRC to horizontal conveyor, hopper, autonomous vehicle, etc.)
Finally, consider the facility-wide implications of fully integrating continuous VRC operation with your existing Warehouse Management Software (WMS), including:
- Bottom-line benefits of full integration vs. stand-alone operation
- Additional costs involved in fully integrating VRCs into your WMS
- Likely returns on investment over time
Detailed Integration Plan
Your initial assessments will provide a roadmap to the critical tasks and potential sticking points your VRC integration will involve. Use it to develop a detailed integration plan to guide how your team works with equipment suppliers and process specialists.
Your plan needs to consider:
- Physical compatibility: This includes ensuring your VRC has the size and weight capacity as well as the design capacity needed to work with existing conveyor systems or fully automated robotic pick and place systems.
- Electrical compatibility: This includes ensuring your VRC can work off your existing electrical systems, including high voltage systems, and two- or three-phase supplies, while including critical breaker and fail-safe measures.
- Software compatibility: This includes high-level integration with your WMS, like plant-wide monitoring and control systems that manage the speed and loading of the system to prevent and manage bottlenecks and slowdowns.
Now let’s take a look at how VRC system compatibility works for three different types of workflow integration.
1. Conveyor Systems
- Physical integration with existing conveyor systems such as belt or roller conveyors.
- Mechanical and electrical integrations to allow VRCs to operate in phase with existing conveyor workflows including co-ordinated lifting cycles or continuous, timed operation.
- Software integration, including dedicated programmable logic controllers (PLCs) to link your VRC to other associated automated warehouse systems.
2. Pick Modules and Robotic Handling
High-speed robotic picking technologies allow rapid order fulfillment and advanced inventory management around the clock.
The flexibility and customizability of VRCs make them useful for keeping pick systems supplied, while their precision, safety, and reliability make them ideal for working with autonomous mobile robots or vehicles.
VRCs from PFlow Industries can be designed for integration with automated robotic vehicles to enable VRC loading and unloading
3. Full WMS Integration
- Local programmable logic controllers (PLCs) controlling individual VRCs
- Smart sensors and cameras provide real-time workflow feedback
- Customized WMS interfaces offering central control of PLCs, cameras, sensors, and other equipment
Read More: Choosing the Right VRC for Your Fully Automated Warehouse
Workflow Integration: 3 Steps to Success
Getting teams with different goals and areas of expertise on the same page can be a challenge. Make sure your project plan enables space for these three steps to help your people connect technology capacities to your workflow needs.
1. Communication and Coordination
Effective integration applies not just to your equipment, but also to your team. Once work gets underway, different stakeholders must continue to communicate and coordinate their work.
This includes engineers, plant managers, and equipment suppliers, but also physical, mechanical, electrical, and software teams. It’s crucial to ensure specifications align, and timelines and project expectations agree at every stage of the project.
2. Testing and Validation
Every lifting application and every process integration project is different. Effective testing and validation are essential to see that integration is not only effective but is adding to the overall efficiency of your workflow and facility operations.
Reliable equipment suppliers will provide testing, troubleshooting, and validation services as part of their installation package. Be sure your supplier can test and validate their equipment and provide effective solutions to ensure it meets the required specifications.
3. Phased Integration
Many VRC suppliers and integration experts recommend a phased integration program to allow specific solutions to be tested and assessed, and the lessons learned taken on board.
Most facility and operations managers opt to go with simpler integration applications first so that specific handling and control techniques can be developed to provide the building blocks for more sophisticated PLC and WMS interface applications.
Go With PFlow for Optimal VRC Integration
Only PFlow Industries has the technical know-how and broad industry experience to deliver the most challenging VRC integration solutions. Since pioneering the original VRC equipment in the 1970s, we’ve designed and installed units in hundreds of warehousing and distribution centers.
An innovative automation solution, our robust, reliable industrial lifting equipment is a critical component in today’s automated, multi-level fulfillment operations.
Talk to us about your unique automation integration challenges. We’ll work with you to develop a fully customized solution to optimize your material handling operations.
We offer:
- End-to-end support from design to installation
- Quality customized construction and integration services
- Industry-leading safety features and reliability
We also offer ongoing technical support for our equipment, comprehensive parts and training services, and long-term preventative maintenance contracts.
Click below to learn more about how our VRC lifting technology can help you achieve your warehouse automation goals.