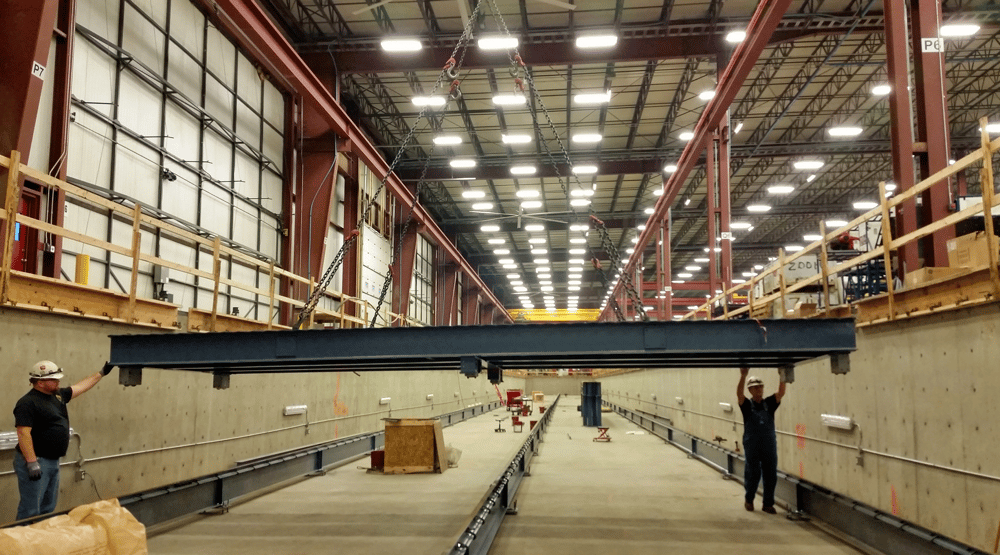
Leading manufacturers of heavy equipment and machinery trust the unrivaled lifting power of vertical reciprocating conveyors (VRCs) for use in their plant operations. Whether lifting pallet-loads, raw materials, or finished products, a VRC can make moving materials around your plant safe and efficient, and they can even be used as part of an automated system that moves materials horizontally and vertically.
What Is a VRC?
A vertical reciprocating conveyor is a specialized lifting solution for moving materials safely and efficiently between different levels in factories, warehouses, distribution centers, hospitals, and other work environments. Powered by either hydraulic or mechanical machinery, VRCs can:
- Lift large, bulky or irregular size loads
- Lift and lower loads weighing from 10 lbs to over 200,000 lbs
- Reach nearly an unlimited number of floor levels
Specifically designed to move materials, not people, VRCs offer superior material handling efficiency and safety while avoiding high maintenance costs and regulatory burdens associated with people-moving elevators. VRCs also:
- Operate indoors, outdoors, and in specialized environments
- Can be installed in new or existing facilities, through floors, in existing elevator shafts, or next to balconies or mezzanines
- Offer smooth travel and stops to ensure even the most sensitive of materials are not damaged
VRCs for Heavy Equipment & Machinery
The capacity, stability, and reliability of VRCs make them the go-to choice for safely lifting the heaviest loads from catalytic scrubbers to huge rolls of bulk paper.
PFlow can design VRCs for confined or hard-to-access areas where forklifts or moveable scissor lifts cannot operate, and all units are equipped with safety gates and enclosures that meet or exceed ASME B20.1 safety standards for conveyors.
PFlow VRCs can be designed to work seamlessly with other materials handling equipment as part of an automated, horizontal to vertical conveyor system.
VRCs and Multi-Directional Movement
The versatile design characteristics of VRCs make them an integral part of an automated material handling system – one that can meet the complex challenges that can come with an automated system designed for use in the manufacture of heavy equipment.
An automated conveyor system that utilizes VRCs, fully integrates horizontal and vertical movements while offering the flexibility of multi-directional VRC loading and unloading patterns that can maximize the use of your facility’s existing space.
A unique example of the use of an automated conveyor system in a manufacturing setting is the custom designed, massive moving-floor assembly line that PFlow engineered in collaboration with Canadian farm machinery giant, Bourgault Industries.
Let’s look at how the inherent strength and reliability of VRC lifting technology was integrated seamlessly into an innovative horizontal moving floor conveyor for assembling heavy agricultural equipment.
Farm-Sized Lifting Solution for Bourgault
When your business is building tillage equipment weighing in at more than 75,000 pounds and sometimes measuring more than 125 square feet, you need a serious assembly line that offers unlimited access to tools and components while keeping production moving.
Bourgault envisaged a dedicated moving-floor assembly line for their 184,000-foot purpose-built manufacturing facility in St Brieux, Saskatchewan, using a string of rail-mounted 25’ x 10’ steel plates powered by hydraulic cylinders. The problem was finding a provider with the technology and know-how to build a return system for the line’s 46 9,000-pound steel carts.
“We consulted with a number of system manufacturers, but none could provide a solution to meet our needs because the sheer size and weight of our tillage equipment exceeded their systems’ capabilities,” explained a lead engineer on the project.
Going Sideways
“PFlow initially caught our interest because of the company’s existing product line of vertical lifts. We were looking for a solution to lower the carts once they had reached the end of the line and then raise them back up at the front of the line so they could be reused after being transferred underneath the system.”
Bourgault’s design team found PFlow was more than willing to take their technology in a new direction to meet their design needs.
“Not only was PFlow able to design a custom down and up lift solution that fit our needs, but the company also engineered the entire moving-floor assembly system, based on our initial design concept, then manufactured and installed it.”
PFlow immediately set to work with Bourgault to include a 496-foot long, nine-foot deep concrete-lined pit in the foundations of the new building to house the return system, allowing the entire assembly system to sit flush with the assembly facility’s floor.
Pushing Further
The heart of the system is, however, a two-stage hydraulic pusher assembly designed by PFlow’s engineers. The servo-based assembly uses feedback from one cylinder to slowly hand over power to a second cylinder, enabling carts to be added continuously to the line while keeping almost one million pounds of floor assembly space moving smoothly.
The floor is designed to support a total load of up to 200,000 lbs and travel between four inches and 3.25 ft per hour, allowing a full transition between one hour and 45 minutes, and 45 hours. Two fully integrated VRCs lower and raise carts four feet at the beginning and end of the return cycle.
The system is also precision-engineered to ensure that deflection between cart edges is never more than 1/8 inch to avoid presenting a trip hazard to assembly workers, while a safety latch system prevents the cart on the floor from separating by more than 1.4 inches.
Bourgault estimates the system has increased productivity in its assembly plant by 30% by allowing tools and components to be staged where they are needed and allowing workers full access to equipment while it is moved.